2025年3月31日,“2025工程机械绿智生态创新大会”在北京盛大举行。这是一场意义非凡的行业盛会,聚焦于“绿智”“生态”“创新”三大关键词,为工程机械行业的可持续发展描绘了清晰的蓝图。“绿智”,即绿色与智能的深度融合,代表着工程机械行业在节能减排、低碳环保的基础上,通过智能化技术提升设备性能与工作效率,实现产业升级与可持续发展;“生态”则强调行业倡导构建绿色供应链,打造可持续发展的产业生态系统;而“创新”是驱动行业变革的核心动力,涵盖技术创新、产品创新、商业模式创新等多个层面,为工程机械行业注入源源不断的活力,助力企业在激烈的市场竞争中脱颖而出。
陕西同力重工股份有限公司技术发展部杜腾部长在大会现场,做了以《在非公路矿用车智能线控系统在矿区运输场景下的应用与前景》为主题的精彩演讲。
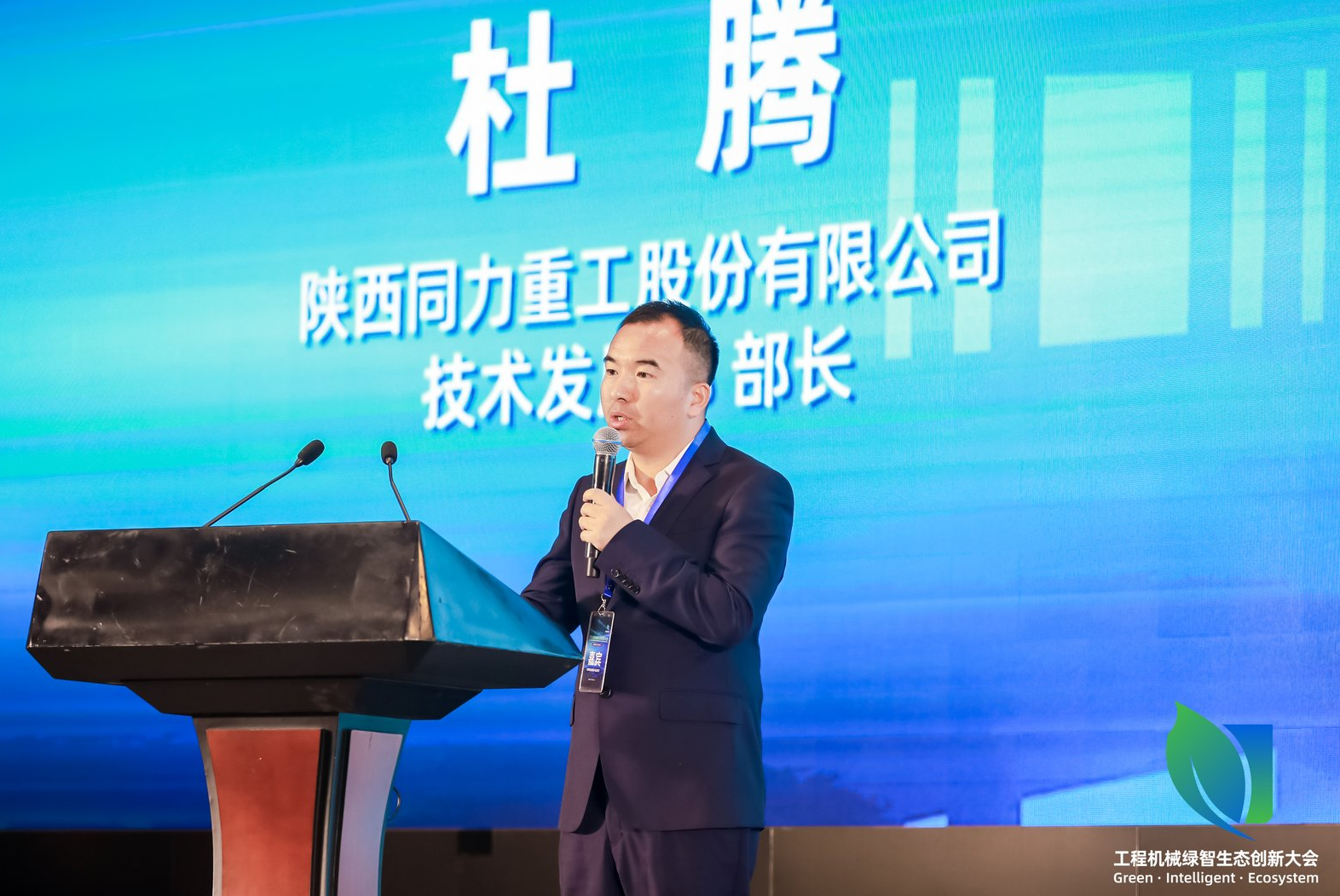
从“经济适用”到“场景定制”的深度实践
在露天矿运输领域,矿卡承担着近95%的物料运输任务,但高油耗、高维护成本与复杂工况的适配问题长期困扰行业。
陕西同力重工以“做最经济适用的非公路用车”为核心理念,提出“全生命周期成本最优”设计准则:通过模块化底盘结构、新能源动力适配(纯电/混动/甲醇增程)及关键零部件寿命优化,实现单台车燃油成本降低10%-15%,维保周期延长30%。其独创的“同力工法”将技术落地分解为五大环节——工况调研、需求分解、方案设计、产品交付和持续改进,形成“一矿一策”定制能力。
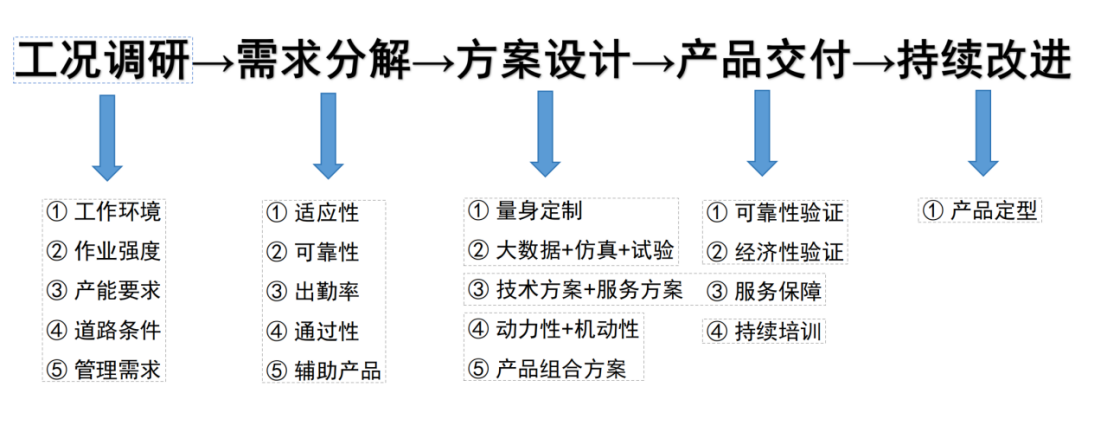
传统矿山四大痛点与智能化转型的必然
当前矿山行业正面临多重挑战。在安全层面,国内矿山安全事故年均直接损失超20亿元,且法规要求事故车辆停运整改周期长达3-6个月;人力层面,矿区驾驶员平均年龄超45岁,年轻从业者缺口率高达60%;成本层面,人工与燃油成本占比运输总费用超70%,不规范操作导致车辆大修率增加40%;而在环境层面,浅层资源枯竭迫使开采向深部拓展,传统机械在坡度超30%、弯道半径不足8米的极限工况下效率骤降。
自2015年起,法律法规、地方政府政策密集出台,为露天矿山运输解决方案的转型指明方向,即大型化、绿色化、智能化。对此,同力重工提出了“无人化并非替代人力,而是重构运输生态”的转型逻辑:通过智能线控技术将司机从危险、重复劳动中解放,转而聚焦调度与运维,同时以标准化作业降低人为失误,最终实现“从少人化到无人化再到全链路智能化”的阶梯升级。
线控关键技术发展现状
作为国内首个实现线控底盘量产的企业,同力重工的关键技术涵盖车辆线控化改造、智能控制系统、故障诊断与安全保护等,成功实现了矿区运输从“有人驾驶”向“无人驾驶”的转型。
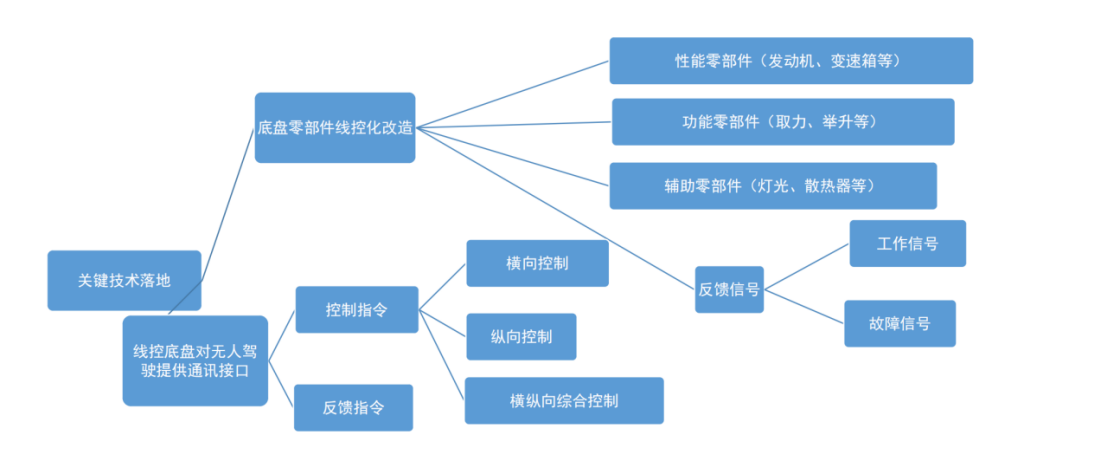
目前,同力重工已与近20家无人驾驶公司合作,累计交付超1000台线控产品,应用场景覆盖煤矿、金属矿及砂石骨料等领域,典型案例包括新疆红沙泉煤矿300余台无人驾驶车辆运行、西藏巨龙铜矿与华为合作项目等。
国内外非公路无人驾驶自卸车发展现状及前景
自2020年至2024年底,中国矿区无人驾驶车辆实现了从零到2700台的爆发式增长,增速显著领先于海外市场(如澳大利亚28年仅积累1400台)。这一增长主要受益于三大驱动因素:一是政策持续推动,2015年起国家密集出台大型化、绿色化、智能化指导文件;二是企业创新合作模式;三是本土成本优势,尤其在低线控技术门槛领域。
尽管无人驾驶能通过24小时不间断作业提升效率,并降低燃料与维护成本,但目前仍面临装卸环节效率低于人工、人机混跑场景技术未完全突破等瓶颈。此外,中国矿区无人驾驶行业亟需解决技术碎片化问题,演讲中,杜鹏呼吁由行业协会牵头制定统一线控标准与协议,通过技术协同推动规模化应用,最终释放矿区无人驾驶的长期价值。
2025 CM GIEI | 杜腾:非公路矿用车智能线控系统在矿区运输场景下的应用与前景
匠客工程机械 评论(0)
来源:匠客工程机械
2025年3月31日,“2025工程机械绿智生态创新大会”在北京盛大举行。这是一场意义非凡的行业盛会,聚焦于“绿智”“生态”“创新”三大关键词,为工程机械行业的可持续发展描绘了清晰的蓝图。“绿智”,即绿色与智能的深度融合,代表着工程机械行业在节能减排、低碳环保的基础上,通过智能化技术提升设备性能与工作效率,实现产业升级与可持续发展;“生态”则强调行业倡导构建绿色供应链,打造可持续发展的产业生态系统;而“创新”是驱动行业变革的核心动力,涵盖技术创新、产品创新、商业模式创新等多个层面,为工程机械行业注入源源不断的活力,助力企业在激烈的市场竞争中脱颖而出。
陕西同力重工股份有限公司技术发展部杜腾部长在大会现场,做了以《在非公路矿用车智能线控系统在矿区运输场景下的应用与前景》为主题的精彩演讲。
从“经济适用”到“场景定制”的深度实践
在露天矿运输领域,矿卡承担着近95%的物料运输任务,但高油耗、高维护成本与复杂工况的适配问题长期困扰行业。
陕西同力重工以“做最经济适用的非公路用车”为核心理念,提出“全生命周期成本最优”设计准则:通过模块化底盘结构、新能源动力适配(纯电/混动/甲醇增程)及关键零部件寿命优化,实现单台车燃油成本降低10%-15%,维保周期延长30%。其独创的“同力工法”将技术落地分解为五大环节——工况调研、需求分解、方案设计、产品交付和持续改进,形成“一矿一策”定制能力。
传统矿山四大痛点与智能化转型的必然
当前矿山行业正面临多重挑战。在安全层面,国内矿山安全事故年均直接损失超20亿元,且法规要求事故车辆停运整改周期长达3-6个月;人力层面,矿区驾驶员平均年龄超45岁,年轻从业者缺口率高达60%;成本层面,人工与燃油成本占比运输总费用超70%,不规范操作导致车辆大修率增加40%;而在环境层面,浅层资源枯竭迫使开采向深部拓展,传统机械在坡度超30%、弯道半径不足8米的极限工况下效率骤降。
自2015年起,法律法规、地方政府政策密集出台,为露天矿山运输解决方案的转型指明方向,即大型化、绿色化、智能化。对此,同力重工提出了“无人化并非替代人力,而是重构运输生态”的转型逻辑:通过智能线控技术将司机从危险、重复劳动中解放,转而聚焦调度与运维,同时以标准化作业降低人为失误,最终实现“从少人化到无人化再到全链路智能化”的阶梯升级。
线控关键技术发展现状
作为国内首个实现线控底盘量产的企业,同力重工的关键技术涵盖车辆线控化改造、智能控制系统、故障诊断与安全保护等,成功实现了矿区运输从“有人驾驶”向“无人驾驶”的转型。
目前,同力重工已与近20家无人驾驶公司合作,累计交付超1000台线控产品,应用场景覆盖煤矿、金属矿及砂石骨料等领域,典型案例包括新疆红沙泉煤矿300余台无人驾驶车辆运行、西藏巨龙铜矿与华为合作项目等。
国内外非公路无人驾驶自卸车发展现状及前景
自2020年至2024年底,中国矿区无人驾驶车辆实现了从零到2700台的爆发式增长,增速显著领先于海外市场(如澳大利亚28年仅积累1400台)。这一增长主要受益于三大驱动因素:一是政策持续推动,2015年起国家密集出台大型化、绿色化、智能化指导文件;二是企业创新合作模式;三是本土成本优势,尤其在低线控技术门槛领域。
尽管无人驾驶能通过24小时不间断作业提升效率,并降低燃料与维护成本,但目前仍面临装卸环节效率低于人工、人机混跑场景技术未完全突破等瓶颈。此外,中国矿区无人驾驶行业亟需解决技术碎片化问题,演讲中,杜鹏呼吁由行业协会牵头制定统一线控标准与协议,通过技术协同推动规模化应用,最终释放矿区无人驾驶的长期价值。
敬请关注 《工程机械与维修》&《今日工程机械》 官方微信
更多精彩内容,请关注《工程机械与维修》与《今日工程机械》官方微信