全球重工行业第一座灯塔工厂。
这是三一重工对中国装备制造的贡献,也是对世界重工行业的贡献。
按照达沃斯世界经济论坛和麦肯锡咨询公司共同的遴选标准,灯塔工厂意味着是“数字化制造”和“全球化4.0”示范者,代表当今全球制造业领域智能制造和数字化最高水平。
9月27日,世界经济论坛(WEF)正式发布新一期全球制造业领域灯塔工厂名单,三一重工北京桩机工厂(下称“北京桩机工厂”)成功入选,成为全球重工行业首家获认证的灯塔工厂。获评世界灯塔工厂,体现出三一重工在先进制造、数字化转型的卓越成果和“领头羊”实力,标志着三一重工在第四次工业革命的竞争中赢得先机。
三一集团董事、高级副总裁代晴华表示,灯塔工厂的建设只是一个起点,未来希望三一能够代表中国制造的最高水平,也希望三一能够站在世界之巅。
目前,三一重工已是全球领先的装备制造企业,2020年以利润全球行业第二、人均产值全球行业第一的业绩迈入高质量发展通道,三一集团整体销售额达到1368亿元。面对汹涌而来的工业4.0浪潮,三一集团董事长梁稳根认为,三一的新使命,就是要成为智能制造的先驱,用新的行动推动中国从制造大国变成制造强国。
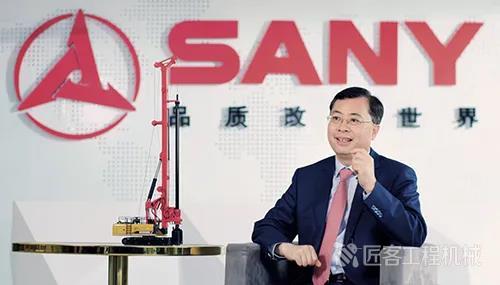
三一集团董事、高级副总裁代晴华
“我们的目标是100名工人,100亿产值”
2018年3月13日,三一集团董事长梁稳根对外公开表示:“三一的数字化转型,要么翻身,要么翻船!”
2019年6月,三一集团引入三现数据集控,柔性生产岛等新型生产方式,启动灯塔工厂等智能单位的建设,推动互联网、大数据、人工智能和制造业深度融合。
这是一场轰轰烈烈、极为不易的变革。
三一重工智能制造研究院院长董明楷介绍,作为重型装备工厂,北京桩机工厂改造之前的生产模式属于典型的离散制造,各零部件加工过程相互独立、互不配合,生产线之间无法衔接。同时,工厂生产设备繁多,内网主要使用WiFi、老旧五类线、光纤,布线复杂,往往牵一发而动全身,部署和调整周期长,成本高。
2019年6月,北京桩机工厂启动改造项目,全面引入5G技术,探索5G技术与工业领域的深度融合。
通过部署上行容量在1Gpbs/万平方米以上、单终端达到300Mbps以上、时延在20ms左右的5G虚拟专网,北京桩机工厂将8个柔性工作中心、16条智能化产线、375台全联网生产设备、上千台水电油气仪表实现全连接,整个工业制造全流程高效互联互通。
树根互联股份有限公司是三一集团灯塔工厂的工业互联网平台服务商,树根互联副总裁刘伟光介绍:“在北京桩机工厂大概有36000多数据点实时接入,通过大数据的算力,实时计算,我们为每一道工序、每一种机型,甚至每一个道具来匹配最优的参数,优化生产能力。”
以桩机下料区切割机为例,改造前,工厂中5台等离子切割机需要5名人员现场操作,不仅作业现场环境差,而且存在人身安全方面的风险。
通过5G+工业互联网建立管理驾驶舱后,8台激光切割机只需两人巡检,而且现场情况通过5G视频和工业互联网数据实时回传,加工任务的开始、复位等操作均可远程无人化操作,远程控制延时低于10ms,实现切割下料安全、高效的无人化作业。
在装配柔性岛,重达数吨的桩机动力头正在这里组装,依托5G高清传感器,重载机器人准确地将大件送入机台,几分钟内就实现了精准组对,误差仅0.3毫米。而在过去,这道工序只能靠人工“吊龙门”完成,不仅劳动强度大,效率也比较低。
“这样超大部件的无人化装配,在行业尚无先例。”董明楷介绍,5G高清传感器就是机器的“慧眼”,每秒可产生100万个三维数据坐标,拥有强大的感知和运算能力,“有了它,无论什么型号的大大小小零件,机器人都能实时得到场景深度信息和三维模型,作业时自动修复偏差”。
目前,这一条柔性装配线可以满足3吨到16吨所有动力头的生产,自动化率达70%,产能翻倍,因磕碰导致的质量缺陷已全部杜绝。
在焊接工作岛内也是同样的场景。机器人通过激光“观察”坡口环境,自动适应调整参数,一次性实现厚40mm、宽60mm的高强钢多层单道焊接,解决了钻杆方头焊接这一全球行业难题。
现场工人表示,机器人相当聪明,焊缝的位置存在偏差,焊接方法就会立即调整,且质量不会有任何偏差。
目前,工厂里小到一块钢板的分拣,大到10多吨桅杆装配,已全部可由机器人自动化完成。北京桩机工厂工艺工程师侯勤华介绍:“机器视觉系统,真正赋予了机器适应环境、柔性完成任务的能力。”数据显示,较改造前,工厂焊接、装配、机加等核心工序作业效率分别提升130%、100%、68%,在同样的厂房面积产值翻了一番。
18年前,当时年仅18岁就来这里做钳工的北京桩机制造管理经理夏闻世表示,以前装配螺栓靠人一个一个地放上去,一个一个地拧紧,再一个一个地手动检测,一个力矩不到位就要返工,“现在,从螺栓抓取、放置、拧紧,实现全自动化,而且自动化防错,那效率翻了不知道多少倍”。
智能制造带来的是生产效率的飞跃。北京桩机灯塔工厂生产节拍加快了不止4倍,7天就能交付一台旋挖钻机,月产能更是翻了一番达到300台,现代化、无人化、自动化、数字化、智能化在这里得到了集中的搭配与融合。
三一集团高级副总经理、北京三一智造科技有限公司总经理李梁健表示,2020年,北京桩机工厂销售78亿元,比2019年增长59%,总体生产设备作业率从66.3%提升到86.7%,平均故障时间下降58.5%,“现在还在不断升级改造”。
2020年,三一重工利润居行业全球第二,人均产值超过全球工程机械“老大”卡特彼勒,跃居行业第一,北京桩机工厂的人均产值更是高达1072.8万元。
三一重工远不满足于此。代晴华称,未来,在北京桩机灯塔工厂要实现百人百亿的高效率目标。
三一重工总裁向文波介绍,三一集团正在加速推动数字化转型,3000名产业工人,实现3000亿元销售额,是未来5年的目标。
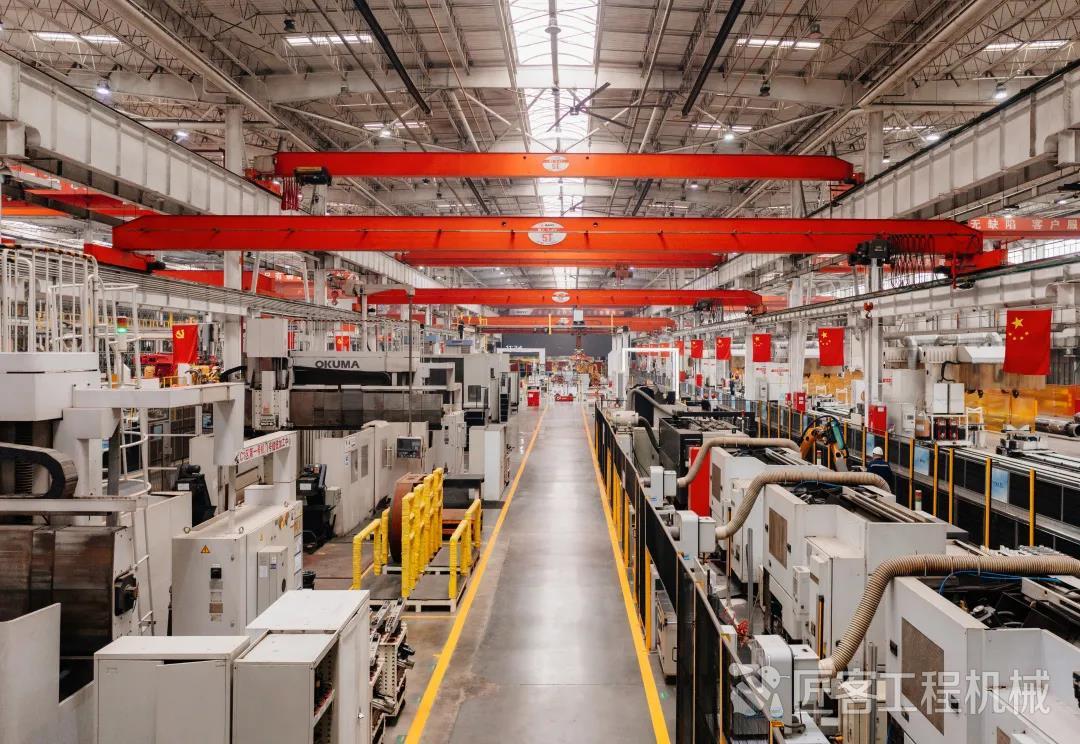
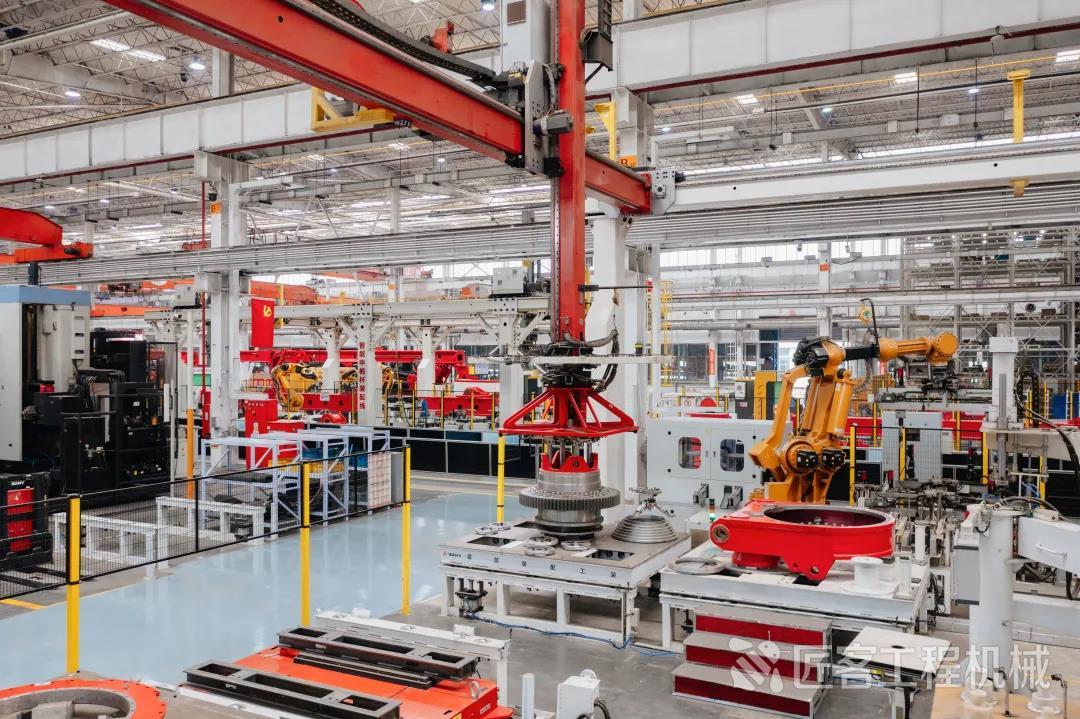
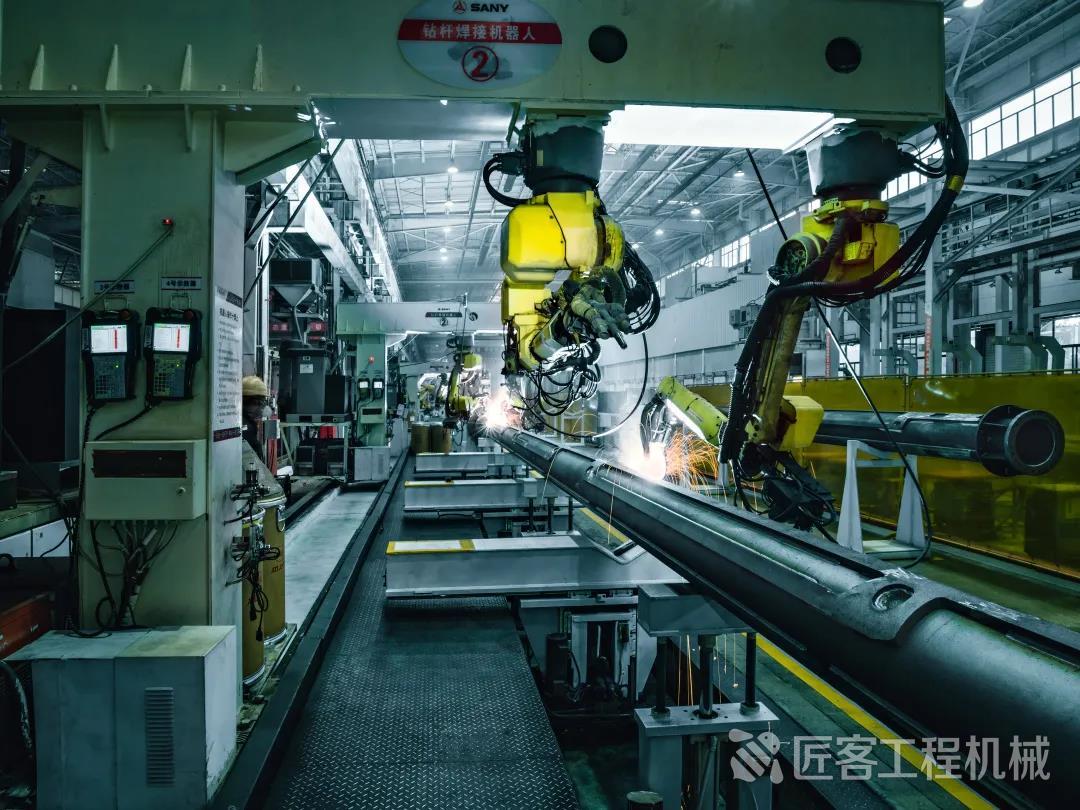
三一重工北京桩机“灯塔工厂”实景
灯塔工厂最大的意义是
机器让人变得更好,人让机器变得更好
灯塔工厂带来的不仅是效率的提升和产能的翻倍。值得重视的是,在三一的灯塔工厂里,工人与机器设备的关系正在悄然发生着改变。
代晴华认为,灯塔工厂最大的意义,并不是让机器取代人,而是机器让人变得更好,人让机器变得更好。
夏闻世说:“以前做装配钳工,干的是重体力活,人确实很累,效率也不高,随着机器设备不断升级,人也越来越轻松,现在做装配,主要是看机器。”
董明楷告诉《中国经济周刊》记者,2018年时,焊工裹得严严实实,带着焊枪和喷枪,在高温、粉尘的环境里工作,“他们是真的不容易”。改造以后,“稍微有点操作经验的工人,通过培训,适当学一些编程,就可以操作机械手,工作环境已经非常好了”。
“在工厂内,基于5G+AR设备的‘人机协同’技术已得到广泛应用。物料分拣、销轴装配等传统劳累活、危险活不再需要人力操作,全部由机器人高效完成。”董明楷说。
不光是让工人从繁重的体力劳动中解放出来,代晴华指出:“现在,智能制造在数字时代帮助我们的生产效能得到了极大的提升,解决了很多的劳动力问题,而与此同时,节省下来的劳动力,又可以把重点放在人工智能的维护和运用以及人类经验的传承上。”
代晴华介绍,旋挖钻机转杆上面的一个对接焊口焊接难度非常高,原来的400多名焊工中只有两位工人能够承担这项任务,因此,他们成为全厂重点保护对象,生产很忙的时候,这两位工人必须加班加点工作,否则转杆就会供不应求,整个工厂的生产进度就被拖住。“他退休以后谁来干这个活呢?老工人的技巧怎么传承下去呢?”代晴华说。
现在,人工智能彻底突破这一瓶颈。
董明楷介绍:“我们的做法是把所有工人的经验,实现参数化和软件化,固化到机器人里。”同时,通过强大的人机协同,机器人AI还能学习熟练工人的技能和手法,并作为教具“以老带新”,最终实现技能传授和工厂“老师傅”工匠精神的传承。“这个核心焊接工序的产能,取得了数十倍的增长。”代晴华接受《中国经济周刊》记者采访时说。他表示,走过这一步之后,原来的工人转型成为工程师,机器负责干活,人负责创新,而人的创新为机器的效率提供了持续不断的进步的可能。“所以,我们说灯塔工厂让人和机器之间形成了一种协同关系,而不仅仅是一个体力的替代关系。”他说。
三一提出的目标是,从现在的30000名工人向30000名工程师转变,培养出历史上最优秀的产业工程师。
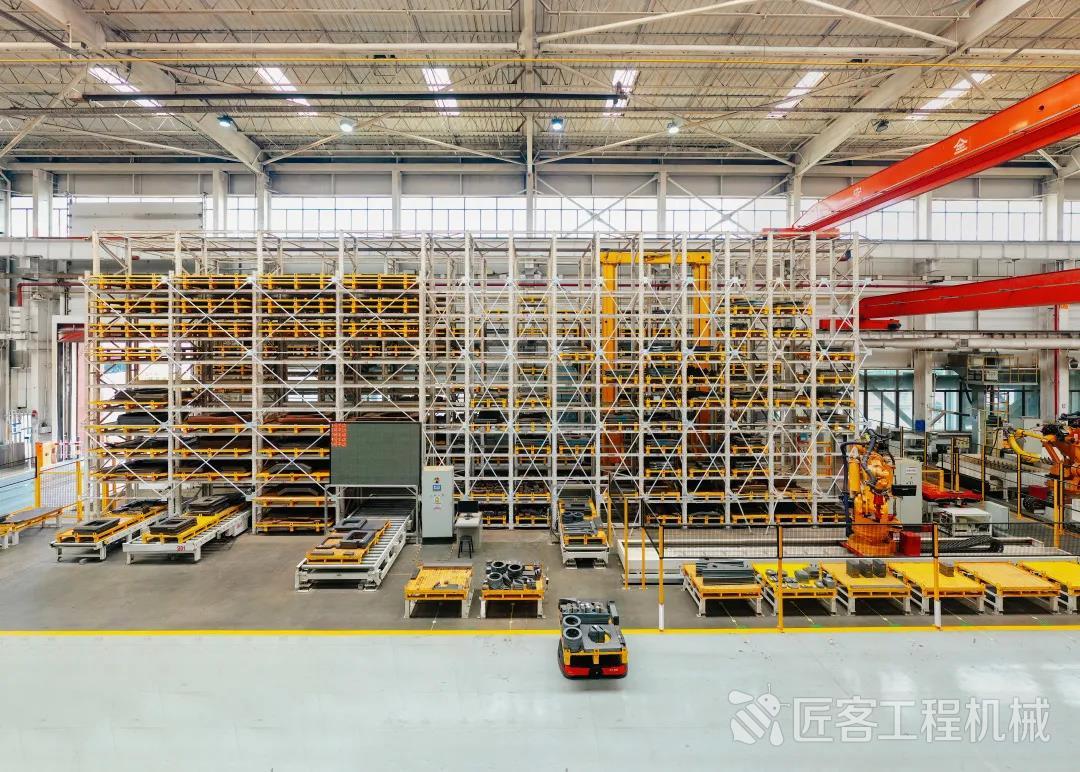
三一重工北京桩机“灯塔工厂”实景
穿越周期,“‘中国制造’已经开始领先了”
在三一集团董事长梁稳根看来,北京桩机工厂成为世界灯塔工厂,是三一的新名片,是三一数字化转型的里程碑,是三一成为智能制造先驱的关键一步。
自2018年启动数字化转型以来,三一集团灯塔工厂建设已经投入达150亿元。代晴华介绍:“灯塔工厂的未来发展,我们已经做了很详细的规划,首先是把三一集团全国乃至全球的40多家工厂,一个一个升级到北京桩机灯塔工厂一样的水平。同时,还要启动重点工厂,比如说北京桩机工厂,进一步升级到3.0的水平,也就是从制造生产的智能化,要全面走向以数字驱动的生产管理的智能化,以及物流配送的智能化,这是已经启动的灯塔工厂3.0规划。”
身处工程机械这一周期性比较强的行业,梁稳根还指出,数字化是穿越周期的法宝。
董明楷对《中国经济周刊》说:“工程机械是典型的离散制造,在行业周期里面,繁荣期需要大量人员,低谷期往往需要控制人员数量。这就导致制造成本高,市场响应速度慢。当市场需求起来的时候,生产能力跟不上;当生产能力上来,市场需求可能过去了。”
初步完成智能制造改造以后,北京桩机工厂在市场波动前就颇为淡定。董明楷表示,桩工机械今年前几个月都是淡季,工厂不需要裁员;四季度生产旺季来了,也不需要招人,只要开动机器,产能就上来了。
代晴华指出,完成智能制造改造以后,三一就摆脱了周期的束缚。2011年,三一集团的员工7万余名,其中一半以上是工人,销售额最高是750亿元。随着智能制造程度的不断深化,2020年销售额是上个周期峰值的一倍以上,达到了1368亿元,一线工人却减少了一半多。“如果未来3000人完成3000亿元,我们基本上不会受周期的影响了。”
梁稳根认为,穿越工程机械行业周期的另一个法宝是国际化。
2021年上半年,三一集团国际销售收入同比大幅增长80%,其中,增幅超过100%的国家地区有50个,包括法国、俄罗斯、印度、越南等。
李梁健认为,之所以能实现如此高速的增长,智能制造提升三一产品的全球竞争力是重要因素。“跟国际同行来比,三一的制造与数字化水平已经处于领先水平,至少是同一位置。”李梁健说。
向文波表示:“我们希望通过三五年的努力在海外再造一个三一重工。过去我们重点放在发展中国家,像非洲、东南亚、南美的一些国家;下一步,我们将把重点放到发达国家,包括美国、澳大利亚、加拿大和一些欧洲国家。”
在谈到三一数字化转型的未来规划时,代晴华透露,三一集团的智能制造模式已经开启了全球化的布局,包括美国工厂都会采用三一桩机的灯塔工厂方式来建设。
代晴华还谈到,不久前,三一美国工厂建设方案来了一次中外PK。一个方案是由日本企业的专家做出来的,另一个是三一自己的灯塔工厂方案。“一比,我们惊讶地发现,‘中国制造’已经开始领先了。他们做的方案里面光是管理人员,就是我们设计方案里管理人员的3~5倍。”
目前,中国已经是全球灯塔工厂数量最多的国家,三一重工北京桩机灯塔工厂是重工行业第一座灯塔工厂。
基于这一成功模式,李梁健说:“不仅是在三一集团铺开智能制造灯塔工厂的建设,我们也在向行业输出智能制造,为供应链端、客户端提供智能制造的升级服务。帮助他们去提升效率,帮助他们降低成本,帮助他们改善质量。事实上,降低他们的成本,提升他们的质量,也是帮助我们提升了竞争力。”
然而,相对于三一集团150亿元的投入规模,众多中小型制造企业能否承担向智能制造升级的成本?
代晴华算了一笔账,三一集团的150亿元看起来投入很大,但是分解到每个单元是能承受的。在北京,一个工人的人工成本,工资加上五险一金等福利,一年基本上要20万元,3年就是60万元,而且工资每年还上涨。“我们机器人是多少价格呢?便宜的大概10多万,贵的60万~70万。一个机器人工作站造价便宜的五六十万,贵的100多万,算下来一般3年左右可以收回改造的费用。”代晴华说。
在树根互联股份有限公司副总裁刘伟光看来,无论是三一集团,还是处于1.0状态的中小企业,都能够享受到智能制造的赋能。
事实上,北京桩机灯塔工厂也可以说是在1.0状态起步。代晴华坦言,2019年改革之前,工厂大量的设备都是老旧设备,是“聋、哑、傻”,“既没有数据输出不能说话,也听不懂什么指令,是‘聋’,更不要说它有什么系统,就是‘傻’”。
通过树根互联的“根云平台”连接起这些“聋、哑、傻”设备之后,代晴华说:“连起来还是有巨大的作用,把所有设备的利用率提升到了67%。”
代晴华预测,3到5年内,中国的中小企业将普遍能够享受工业互联网,特别是5G技术带来的无线工业互联网智能制造的成果,真正实现由制造大国转向制造强国。
“智造”三一,共创未来
匠客工程机械 评论(0)
来源:匠客工程机械
全球重工行业第一座灯塔工厂。
这是三一重工对中国装备制造的贡献,也是对世界重工行业的贡献。
按照达沃斯世界经济论坛和麦肯锡咨询公司共同的遴选标准,灯塔工厂意味着是“数字化制造”和“全球化4.0”示范者,代表当今全球制造业领域智能制造和数字化最高水平。
9月27日,世界经济论坛(WEF)正式发布新一期全球制造业领域灯塔工厂名单,三一重工北京桩机工厂(下称“北京桩机工厂”)成功入选,成为全球重工行业首家获认证的灯塔工厂。获评世界灯塔工厂,体现出三一重工在先进制造、数字化转型的卓越成果和“领头羊”实力,标志着三一重工在第四次工业革命的竞争中赢得先机。
三一集团董事、高级副总裁代晴华表示,灯塔工厂的建设只是一个起点,未来希望三一能够代表中国制造的最高水平,也希望三一能够站在世界之巅。
目前,三一重工已是全球领先的装备制造企业,2020年以利润全球行业第二、人均产值全球行业第一的业绩迈入高质量发展通道,三一集团整体销售额达到1368亿元。面对汹涌而来的工业4.0浪潮,三一集团董事长梁稳根认为,三一的新使命,就是要成为智能制造的先驱,用新的行动推动中国从制造大国变成制造强国。
三一集团董事、高级副总裁代晴华
“我们的目标是100名工人,100亿产值”
2018年3月13日,三一集团董事长梁稳根对外公开表示:“三一的数字化转型,要么翻身,要么翻船!”
2019年6月,三一集团引入三现数据集控,柔性生产岛等新型生产方式,启动灯塔工厂等智能单位的建设,推动互联网、大数据、人工智能和制造业深度融合。
这是一场轰轰烈烈、极为不易的变革。
三一重工智能制造研究院院长董明楷介绍,作为重型装备工厂,北京桩机工厂改造之前的生产模式属于典型的离散制造,各零部件加工过程相互独立、互不配合,生产线之间无法衔接。同时,工厂生产设备繁多,内网主要使用WiFi、老旧五类线、光纤,布线复杂,往往牵一发而动全身,部署和调整周期长,成本高。
2019年6月,北京桩机工厂启动改造项目,全面引入5G技术,探索5G技术与工业领域的深度融合。
通过部署上行容量在1Gpbs/万平方米以上、单终端达到300Mbps以上、时延在20ms左右的5G虚拟专网,北京桩机工厂将8个柔性工作中心、16条智能化产线、375台全联网生产设备、上千台水电油气仪表实现全连接,整个工业制造全流程高效互联互通。
树根互联股份有限公司是三一集团灯塔工厂的工业互联网平台服务商,树根互联副总裁刘伟光介绍:“在北京桩机工厂大概有36000多数据点实时接入,通过大数据的算力,实时计算,我们为每一道工序、每一种机型,甚至每一个道具来匹配最优的参数,优化生产能力。”
以桩机下料区切割机为例,改造前,工厂中5台等离子切割机需要5名人员现场操作,不仅作业现场环境差,而且存在人身安全方面的风险。
通过5G+工业互联网建立管理驾驶舱后,8台激光切割机只需两人巡检,而且现场情况通过5G视频和工业互联网数据实时回传,加工任务的开始、复位等操作均可远程无人化操作,远程控制延时低于10ms,实现切割下料安全、高效的无人化作业。
在装配柔性岛,重达数吨的桩机动力头正在这里组装,依托5G高清传感器,重载机器人准确地将大件送入机台,几分钟内就实现了精准组对,误差仅0.3毫米。而在过去,这道工序只能靠人工“吊龙门”完成,不仅劳动强度大,效率也比较低。
“这样超大部件的无人化装配,在行业尚无先例。”董明楷介绍,5G高清传感器就是机器的“慧眼”,每秒可产生100万个三维数据坐标,拥有强大的感知和运算能力,“有了它,无论什么型号的大大小小零件,机器人都能实时得到场景深度信息和三维模型,作业时自动修复偏差”。
目前,这一条柔性装配线可以满足3吨到16吨所有动力头的生产,自动化率达70%,产能翻倍,因磕碰导致的质量缺陷已全部杜绝。
在焊接工作岛内也是同样的场景。机器人通过激光“观察”坡口环境,自动适应调整参数,一次性实现厚40mm、宽60mm的高强钢多层单道焊接,解决了钻杆方头焊接这一全球行业难题。
现场工人表示,机器人相当聪明,焊缝的位置存在偏差,焊接方法就会立即调整,且质量不会有任何偏差。
目前,工厂里小到一块钢板的分拣,大到10多吨桅杆装配,已全部可由机器人自动化完成。北京桩机工厂工艺工程师侯勤华介绍:“机器视觉系统,真正赋予了机器适应环境、柔性完成任务的能力。”数据显示,较改造前,工厂焊接、装配、机加等核心工序作业效率分别提升130%、100%、68%,在同样的厂房面积产值翻了一番。
18年前,当时年仅18岁就来这里做钳工的北京桩机制造管理经理夏闻世表示,以前装配螺栓靠人一个一个地放上去,一个一个地拧紧,再一个一个地手动检测,一个力矩不到位就要返工,“现在,从螺栓抓取、放置、拧紧,实现全自动化,而且自动化防错,那效率翻了不知道多少倍”。
智能制造带来的是生产效率的飞跃。北京桩机灯塔工厂生产节拍加快了不止4倍,7天就能交付一台旋挖钻机,月产能更是翻了一番达到300台,现代化、无人化、自动化、数字化、智能化在这里得到了集中的搭配与融合。
三一集团高级副总经理、北京三一智造科技有限公司总经理李梁健表示,2020年,北京桩机工厂销售78亿元,比2019年增长59%,总体生产设备作业率从66.3%提升到86.7%,平均故障时间下降58.5%,“现在还在不断升级改造”。
2020年,三一重工利润居行业全球第二,人均产值超过全球工程机械“老大”卡特彼勒,跃居行业第一,北京桩机工厂的人均产值更是高达1072.8万元。
三一重工远不满足于此。代晴华称,未来,在北京桩机灯塔工厂要实现百人百亿的高效率目标。
三一重工总裁向文波介绍,三一集团正在加速推动数字化转型,3000名产业工人,实现3000亿元销售额,是未来5年的目标。
三一重工北京桩机“灯塔工厂”实景
灯塔工厂最大的意义是
机器让人变得更好,人让机器变得更好
灯塔工厂带来的不仅是效率的提升和产能的翻倍。值得重视的是,在三一的灯塔工厂里,工人与机器设备的关系正在悄然发生着改变。
代晴华认为,灯塔工厂最大的意义,并不是让机器取代人,而是机器让人变得更好,人让机器变得更好。
夏闻世说:“以前做装配钳工,干的是重体力活,人确实很累,效率也不高,随着机器设备不断升级,人也越来越轻松,现在做装配,主要是看机器。”
董明楷告诉《中国经济周刊》记者,2018年时,焊工裹得严严实实,带着焊枪和喷枪,在高温、粉尘的环境里工作,“他们是真的不容易”。改造以后,“稍微有点操作经验的工人,通过培训,适当学一些编程,就可以操作机械手,工作环境已经非常好了”。
“在工厂内,基于5G+AR设备的‘人机协同’技术已得到广泛应用。物料分拣、销轴装配等传统劳累活、危险活不再需要人力操作,全部由机器人高效完成。”董明楷说。
不光是让工人从繁重的体力劳动中解放出来,代晴华指出:“现在,智能制造在数字时代帮助我们的生产效能得到了极大的提升,解决了很多的劳动力问题,而与此同时,节省下来的劳动力,又可以把重点放在人工智能的维护和运用以及人类经验的传承上。”
代晴华介绍,旋挖钻机转杆上面的一个对接焊口焊接难度非常高,原来的400多名焊工中只有两位工人能够承担这项任务,因此,他们成为全厂重点保护对象,生产很忙的时候,这两位工人必须加班加点工作,否则转杆就会供不应求,整个工厂的生产进度就被拖住。“他退休以后谁来干这个活呢?老工人的技巧怎么传承下去呢?”代晴华说。
现在,人工智能彻底突破这一瓶颈。
董明楷介绍:“我们的做法是把所有工人的经验,实现参数化和软件化,固化到机器人里。”同时,通过强大的人机协同,机器人AI还能学习熟练工人的技能和手法,并作为教具“以老带新”,最终实现技能传授和工厂“老师傅”工匠精神的传承。“这个核心焊接工序的产能,取得了数十倍的增长。”代晴华接受《中国经济周刊》记者采访时说。他表示,走过这一步之后,原来的工人转型成为工程师,机器负责干活,人负责创新,而人的创新为机器的效率提供了持续不断的进步的可能。“所以,我们说灯塔工厂让人和机器之间形成了一种协同关系,而不仅仅是一个体力的替代关系。”他说。
三一提出的目标是,从现在的30000名工人向30000名工程师转变,培养出历史上最优秀的产业工程师。
三一重工北京桩机“灯塔工厂”实景
穿越周期,“‘中国制造’已经开始领先了”
在三一集团董事长梁稳根看来,北京桩机工厂成为世界灯塔工厂,是三一的新名片,是三一数字化转型的里程碑,是三一成为智能制造先驱的关键一步。
自2018年启动数字化转型以来,三一集团灯塔工厂建设已经投入达150亿元。代晴华介绍:“灯塔工厂的未来发展,我们已经做了很详细的规划,首先是把三一集团全国乃至全球的40多家工厂,一个一个升级到北京桩机灯塔工厂一样的水平。同时,还要启动重点工厂,比如说北京桩机工厂,进一步升级到3.0的水平,也就是从制造生产的智能化,要全面走向以数字驱动的生产管理的智能化,以及物流配送的智能化,这是已经启动的灯塔工厂3.0规划。”
身处工程机械这一周期性比较强的行业,梁稳根还指出,数字化是穿越周期的法宝。
董明楷对《中国经济周刊》说:“工程机械是典型的离散制造,在行业周期里面,繁荣期需要大量人员,低谷期往往需要控制人员数量。这就导致制造成本高,市场响应速度慢。当市场需求起来的时候,生产能力跟不上;当生产能力上来,市场需求可能过去了。”
初步完成智能制造改造以后,北京桩机工厂在市场波动前就颇为淡定。董明楷表示,桩工机械今年前几个月都是淡季,工厂不需要裁员;四季度生产旺季来了,也不需要招人,只要开动机器,产能就上来了。
代晴华指出,完成智能制造改造以后,三一就摆脱了周期的束缚。2011年,三一集团的员工7万余名,其中一半以上是工人,销售额最高是750亿元。随着智能制造程度的不断深化,2020年销售额是上个周期峰值的一倍以上,达到了1368亿元,一线工人却减少了一半多。“如果未来3000人完成3000亿元,我们基本上不会受周期的影响了。”
梁稳根认为,穿越工程机械行业周期的另一个法宝是国际化。
2021年上半年,三一集团国际销售收入同比大幅增长80%,其中,增幅超过100%的国家地区有50个,包括法国、俄罗斯、印度、越南等。
李梁健认为,之所以能实现如此高速的增长,智能制造提升三一产品的全球竞争力是重要因素。“跟国际同行来比,三一的制造与数字化水平已经处于领先水平,至少是同一位置。”李梁健说。
向文波表示:“我们希望通过三五年的努力在海外再造一个三一重工。过去我们重点放在发展中国家,像非洲、东南亚、南美的一些国家;下一步,我们将把重点放到发达国家,包括美国、澳大利亚、加拿大和一些欧洲国家。”
在谈到三一数字化转型的未来规划时,代晴华透露,三一集团的智能制造模式已经开启了全球化的布局,包括美国工厂都会采用三一桩机的灯塔工厂方式来建设。
代晴华还谈到,不久前,三一美国工厂建设方案来了一次中外PK。一个方案是由日本企业的专家做出来的,另一个是三一自己的灯塔工厂方案。“一比,我们惊讶地发现,‘中国制造’已经开始领先了。他们做的方案里面光是管理人员,就是我们设计方案里管理人员的3~5倍。”
目前,中国已经是全球灯塔工厂数量最多的国家,三一重工北京桩机灯塔工厂是重工行业第一座灯塔工厂。
基于这一成功模式,李梁健说:“不仅是在三一集团铺开智能制造灯塔工厂的建设,我们也在向行业输出智能制造,为供应链端、客户端提供智能制造的升级服务。帮助他们去提升效率,帮助他们降低成本,帮助他们改善质量。事实上,降低他们的成本,提升他们的质量,也是帮助我们提升了竞争力。”
然而,相对于三一集团150亿元的投入规模,众多中小型制造企业能否承担向智能制造升级的成本?
代晴华算了一笔账,三一集团的150亿元看起来投入很大,但是分解到每个单元是能承受的。在北京,一个工人的人工成本,工资加上五险一金等福利,一年基本上要20万元,3年就是60万元,而且工资每年还上涨。“我们机器人是多少价格呢?便宜的大概10多万,贵的60万~70万。一个机器人工作站造价便宜的五六十万,贵的100多万,算下来一般3年左右可以收回改造的费用。”代晴华说。
在树根互联股份有限公司副总裁刘伟光看来,无论是三一集团,还是处于1.0状态的中小企业,都能够享受到智能制造的赋能。
事实上,北京桩机灯塔工厂也可以说是在1.0状态起步。代晴华坦言,2019年改革之前,工厂大量的设备都是老旧设备,是“聋、哑、傻”,“既没有数据输出不能说话,也听不懂什么指令,是‘聋’,更不要说它有什么系统,就是‘傻’”。
通过树根互联的“根云平台”连接起这些“聋、哑、傻”设备之后,代晴华说:“连起来还是有巨大的作用,把所有设备的利用率提升到了67%。”
代晴华预测,3到5年内,中国的中小企业将普遍能够享受工业互联网,特别是5G技术带来的无线工业互联网智能制造的成果,真正实现由制造大国转向制造强国。
敬请关注 《工程机械与维修》&《今日工程机械》 官方微信
更多精彩内容,请关注《工程机械与维修》与《今日工程机械》官方微信